Video beschikbaar voor leden na onze kick-off op 30/03/2022.
Art.#6: TPM - Before & After
In vorige artikels (Art#1, 2 en 3) werd duidelijk gemaakt hoe we de Lean weg insloegen middels Kaizen. Art#5-“Pull, don’t push” toonde aan dat Pull-implementatie dè maatstaf is van Lean-zijn. En reeds in Art#4 werd voorwaarde n°1 behandeld om tot Pull te kunnen komen, nl. korte omsteltijden. Daar stonden we dan, na 2-3 jaar van onze ‘Lean-journey’. Doordat we het zo druk hadden met het uitrollen van SMED en PULL hadden we het zelf nog niet echt in de smiezen, maar bleek dat het ‘Service Level’ naar onze externe klanten niet echt verbeterde.
Geen nood echter. Op het moment dat de workload-emmer bijna overloopt zijn daar altijd de Japanse sensei met een nieuwe uitdaging, en wat voor één. Na een divest-operatie zagen wij ons genoodzaakt om een nieuwe toolshop in te richten. Logisch denkend maakten wij een ruimte vrij aanpalend aan onze spuitgietproductie. Met deze greenfield droomden wij reeds van een state-of-the-art werkplaats voor onze matrijzen. Niet toevallig kwam opper-sensei Nakao op blitzbezoek. Zijn passage blijft bij iedereen die erbij was in het geheugen geprent.
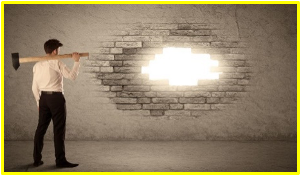
Hij zag de lege ruimte voor de nieuwe toolshop en vroeg … een moker. Yes, a sledge hammer. Ietwat als giechelende pubers kwamen wij ermee op de proppen. Nakao deed wat niemand ooit had kunnen denken. Hij klopte eigenhandig een groot gat in de (Ytong)-muur tussen productie en toolshop. NO WALLS, NO DEPARTMENTS was zijn credo. Punt gemaakt! Zijn dauphin, sensei Kurosaka, maakte het later nog surrealistischer door ons 2 objectieven te geven voor de nieuwe toolshop:
1. “Create Flow”
2. “No more Repairs”
Ik was zeker niet de enige die daar toen verweesd achterbleef met de vraag “Waar heeft die het over?” Flow creëren in een werkplaats, hoe doe je dat in godsnaam? En dan … geen reparaties … hoe komt hij erbij? Dat is net de bestaansreden van onze toolshop.
“You need to change the way you think.” - Taiichi Ohno
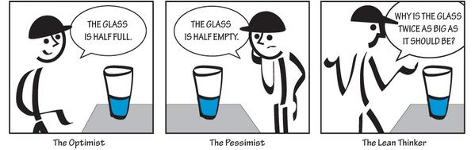
Maar wat was nu alweer het probleem dat moest opgelost worden? Ons Service Level. Dat kregen we niet beter dan zowat 84%. Art Byrne peperde het ons goed in: Iedere dag slagen jullie erin om 15% van concrete klantenorders niet te kunnen produceren cq uitleveren. Reality check. Goal is 98%. Paukenslag!
Bij de eerste Kaizen over dit onderwerp, er zouden er daarna nog méér dan 40 volgen, analyseerden we eerst waarom we zo’n slecht service level hadden. Snel was het duidelijk dat de oorzaak lag bij het niet beschikbaar zijn van in casu machines en matrijzen. In een vorig artikel (Art#4-SMED-vrees) werd het belang van technische standaarden, zonder uitzonderingen, reeds vermeld. Door deze standaardisatie werd het dogma van ‘dedicated’ machine weerlegd. Elke matrijs in een categorie kon nu ook op eender welke machine uit diezelfde categorie produceren. Op zich was dat al een doorbraak, zeker in de mindset van menig productie-engineering-planning medewerker. Onze onderhoudsafdeling kon nu perfect plannen om alle machines periodiek een dag of zelfs een week uit productie te nemen voor preventief onderhoud.
Met matrijzen is het echter een ander verhaal. Voor de meeste te produceren producten is er maar één matrijs voorhanden. Is die er niet, dan is er dus geen productie mogelijk. Wat was de realiteit toen? De matrijzen bleven, bij wijze van spreken, in gebruik tot ze ‘kapot’ gingen. Dan werden die in de (lange) wachtrij van herstellingen gezet. De toen 9-koppige toolshop, enkel werkend in dagploeg, kon amper enkele matrijzen per week herstellen. Onvoldoende. Met dus een ‘day-to-day struggle’ tussen productie en toolshop als gevolg. Sounds familiar? Daar was wél de ‘root cause’ van ons Service level probleem gevonden: Matrijsherstellingen. En was dat nu net niet de sensei doelstelling: No more repairs.
Nog steeds in die eerste Kaizen suggereerde Art Byrne om elke matrijs na elke run een onderhoud te geven. Wij simuleerden een pragmatischer aanpak met een soort van ‘selectief’ preventief onderhoud. Uitkomst was dat de toolshop méér dan 1.000 matrijzen/jaar zou moeten onderhouden/repareren. De reactie van het team liet zich raden: Werf maar 10 man extra aan, koop méér machines en matrijzen, bouw groot onderdelen magazijn, enz … Het kromme wijs-vingertje van Art zei kalm maar overtuigend: No way!
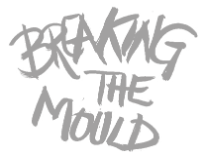
“Breaking the mould” is een Amerikaans gezegde die duidt op een ongewone wijze van denken en doen. Toepasselijk, zo zal blijken. Wij stelden ons tot doel: 100% BESCHIKBAARHEID & 100% BETROUWBAAR. TPM (Total Productive Maintenance) op zijn scherpst, niets minder was nodig om ons Service Level te kunnen verbeteren. Ettelijke Kaizens gingen aanvankelijk over wat preventief onderhoud nu juist moet zijn en hoe die in praktijk te brengen. Weken, zo niet maanden duurde deze ‘clash of minds’. In tegenstelling tot traditioneel management zoeken we bij Lean niet naar “wie” maar wel “wat” de oorzaak is voor, in deze dus, lange rij reparaties.
Wat je op het eerste zicht niet zou verwachten in Kaizens met zo een technische inslag is het gewicht van de factor mens. Weerstand tegen verandering, ijdelheid, ego’s, status-quo behouden, heroïsm, comfortzones, schrik van iets nieuws, helpen en willen geholpen worden, polyvalentie, wij/zij, … de lijst is quasi oneindig en niets menselijks is er vreemd. En dat dit alles in de weg kan zitten wordt duidelijk als je bvb de echte toegevoegde waarde in een preventief onderhoud proces bekijkt. Kuisen en smeren bvb is ‘minderwaardig’ voor pakweg een CNC-frezer, die voelt zich dan nog gesteund door loonschalen en vakorganisaties. Heilige koeien alom.
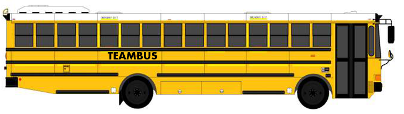
“Get the right people on the bus, the wrong people off the bus and the right people in the right seats.”
Tijdens elke Lean-journey, zegt Art Byrne, is het transformeren van mensen cruciaal. Mopperen of erger nog, hakken in het zand zetten, helpt niemand in zijn of haar toekomstige professionele en persoonlijke ontwikkeling.
“To get something you never had, you have to do something you never did.” – Thomas Jefferson
Proberen, experimenteren dan maar. Door één iemand een dagelijkse kuis en smeerronde in productie te laten doen, bleek ineens het aantal matrijsstoringen significant af te nemen. De achillespees was gevonden. Nog in die vroege Kaizen-fase wees een bezoeker mij er op: Wat is de ‘hands-on-tool’ tijd? Spoorslags zijn we deze gaan meten. Bleek dat onze toolshop medewerkers, stuk voor stuk geschoolde en ervaren technici, amper 15% van hun werktijd aan het doen waren waar ze voor aangeworven waren, nl het onderhouden cq repareren van matrijzen. Betekende dus dat zij 85% van hun tijd bezig waren met “niet toegevoegde waarde” activiteiten. Rondrijden met vorklift en kar, hijskettingen halen, oogvijzen in en uitdraaien, koevoet en voorhamer om matrijzen te openen, hijsen met takel tot en met spectaculaire matrijskantelingen op rubberbanden. Plezant. 😊
Alle gekheid op een stokje natuurlijk, maar wij wisten ineens wel wat ons te doen stond. Onze SMED ervaring bleek van goudwaarde. Naar analogie met wat we in de spuitgietproductie gerealiseerd hebben (zie Art#4). Ook hier een oplossing vinden zonder gebruik te maken van hijskranen, vorkliften, ed … en dat voor matrijzen van 600 tot 6.000 kg. Brrrr …
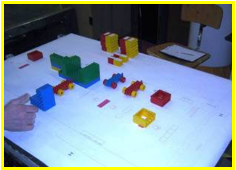
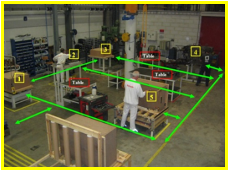
Mijn kinderen waren de Duplo blokjes ontgroeid, dus voor ons uitstekend didactisch materiaal om simulaties te maken van lay-out en … flow, jawel. Tientallen variaties werden bedacht, getest met levensgrote houten of carton mock-up’s. In de VS en Japan noemen ze dit de 3P-fase: Pré-Production-Process. De één na de ander sneuvelde (soms letterlijk). De kritische groepsdynamiek in de Kaizens alsook de sensei waren meedogenloos. Ontelbare praktische bezwaren moesten bedwongen worden, nieuwe (muur)-passages, electrische cabines, niveau verschillen, brandveiligheid, safety, ergonomie, enz … Gaandeweg kristalliseerde de uiteindelijke oplossing zich. Als team, zelfverzekerd en met de knieën op de betonvloer, presenteerden we deze andermaal aan sensei Kurusaka.
“Mmmm … this is just a 30% flow, but OK, go for it”.
Eindelijk hadden we een perspectief, en dit na zoveel mislukkingen bij het bedenken, maken en uittesten van oa een Open-Sluit Pers, Kantelstation, Mobiele werkstations, enz … Niet zelden was enig hoongelach ons deel bij de Gemba toer. Daar en toen hebben wij geleerd dat elke mislukking een leermoment is en … eigenlijk een compliment verdient. Het hoeft waarschijnlijk geen betoog, maar doorzettingsvermogen was toen zowat de beste eigenschap die men kon bezitten, tientallen Kaizens over een 3+ jarige periode volgden nog.
“You only fail when you stop trying.” – Albert Einstein
Uiteindelijk hadden we alle nodige puzzelstukjes, niet zelden kleine technische zaken waar we mini-Kaizens (2-3 personen, 1-2 dagen) voor organiseerden. Kaizen werd zo nog meer ons probleem oplossend model. Geen ‘Off-Gemba’ studiewerk. Tot onze scha en schande hebben wij menigmaal ons lesje geleerd:
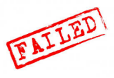
VERMIJD VOOROPGESTELDE PLANNEN.
Altijd zal de ‘doe-realiteit’ op de Gemba U als vanzelfsprekend wijzen welke richting te volgen. Hierbij wordt Nakao-san’s dogma nog maar eens bewaarheid:
“See with your feet. Think with your hands.” – sensei Nakao
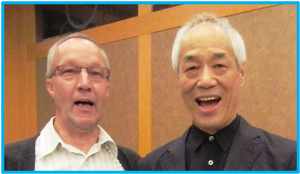
‘Father of moonshine’ Nakao-san aside humble author
De ‘change-over time’, tijd nodig om matrijs vanuit productie tot op de werktafels te brengen, reduceerden we met deze nieuwe FLOW (doel #1) van BEFORE 1,5 uur met 2 tech’s tot een AFTER, alweer single digit, 9 minuten en dat met slechts 1 technieker. Alles loopt nu, letterlijk, op rolletjes.
Herinner je de ‘hands-on-tool’ tijd? Wel de armtierige 15% BEFORE is nu een effectieve 90% AFTER. Was dit een essentiële doorbraak naar doorlooptijdreductie, doel #2 was toch nog steeds om herstellingen te vermijden. Eerder in dit artikel kon U reeds lezen dat kuisen en smeren de hoeksteen is van preventief onderhoud. Tja, PO, iedereen zal wel instemmend knikken, maar wie doet het dan wel zo strikt? 😊
Met de snelle wisseltijden kon er geen sprake meer zijn van een alibi om alsnog door te blijven produceren. Matrijs niet OK = “Stop the line” (Jidoka), terug naar toolshop en “Fix it”. Daar konden we nu op een snelle, veilige en ergonomische manier de bewegende matrijsonderdelen demonteren om die te onderhouden of te vervangen cq te herstellen.
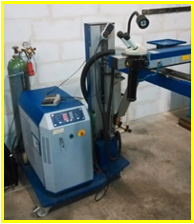
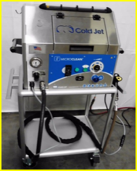
En door middel van strategische investeringen in oa laserlassen, ultrasoon, droogijs, enz … zijn we nu in staat per direct herstellingen uit te voeren. Daar waar we voorheen het onderdeel moesten demonteren en soms buitenhuis laten bewerken. Zo reduceerden wij de reparatietijd van meerdere uren of zelfs dagen tot slechts enkele minuten.
Nieuw en verbeterd Standard Work is altijd één van de resultaten van Kaizen. Ook hier dus, zelfs al betrof het technisch onderhoudswerk. Om onze eigen doelstelling van 100% betrouwbaarheid te kunnen garanderen was een complete eindcontrole van elke matrijs op zijn plaats. Maar ook dat vroeg een adaptieve mindset van onze techniekers. Al dan niet terecht kritiek geven op middelen en mensen is een zwaktebod, daartegenover, ‘ownership’ nemen over eigen werk en resultaat??? Om dit te realiseren suggereerde onze Lean VP een feedback-bord. Na de matrijsopstart moet de productie medewerker een beoordeling geven van elke door de toolshop afgeleverde matrijs. 0% werd in ROOD, 100% in GROEN geschreven. Een beoordeling van hun werk door ‘peers’ en niet door de baas, visueel voor iedereen, werkte stimulerend. Gewoon geniaal.
“If you have to say you’re a lady, you’re probably not” - Margaret Thatcher
De ‘single operator’ doorlooptijd voor onderhoud-herstelling-controle van de meest voorkomende matrijzen (kost ca 100k€) was BEFORE 2 tot 3 dagen, nu AFTER nog 45 minuten tot 1,5 uur. Net doordat alles nu sneller kon, waren we in staat om de matrijzen veelvuldig te onderhouden en dat op zich had tot gevolg dat er veel minder herstellingen moesten plaatshebben.
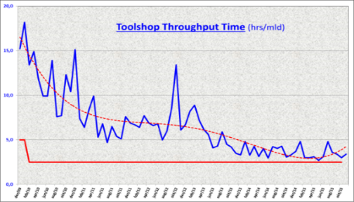
Nu, hoe stuur en ‘trigger’ je zo’n onderhoudsproces? Vroeger was er een dagelijkse meeting tussen de verantwoordelijken van productie en toolshop. Door teveel agendapunten en nodeloze discussies liep die vergadering dikwijls uit waardoor het al snel tegen de middag was vooraleer de opdrachten uitgedeeld werden. Dus komaf daarmee, geen meetings meer, enkel nog een visueel communicatiebord die de status van elke matrijs in REAL TIME weergeeft.
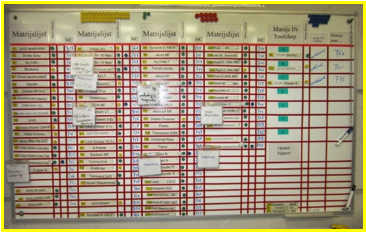
De spuigietproductie is “de klant” van de toolshop. Als in een PULL-systeem bepalen zij op ieder moment van de dag welke matrijs met welke prioriteit moet behandeld worden. De toolshop is een integraal onderdeel op het einde van elke productierun of bij een abnormaliteit. Resultaat is een quasi 100% beschikbaarheid van matrijzen. Ook belangrijk: Nu is er, à la carte, snelheid van interventie.
Zoals bijna elk productiebedrijf hebben ook wij high en low runners. Vooral dankzij de snelle matrijs-wissels kunnen die laatste soms zo kort zijn als een half uur productie. Crazy, hé. 😊 Vanzelfsprekend wordt matrijsonderhoud hier getriggerd door observaties en shotcounters. De langlopende matrijzen daarentegen, moeten per definitie minstens éénmaal/week onderhouden worden. In praktijk is dit niet zelden nog frequenter omdat er inzetstukken kunnen omgewisseld worden (logo, textuur, …). Door ons TPM-proces hebben wij nu een spin-off voordeel in flexibiliteit naar onze klanten. Ook nog: De levensduur van de kostbare matrijzen word daardoor makkelijk met factor 3 verlengd.
Techniekers in de toolshop en bij uitbreiding in onderhoud moet je als het ware zien als ‘dokters’. Zij moeten de patiënt genezen, al dan niet in het ‘hospitaal’. Naar analogie, en in het kader van 5S, steken al onze mensen in een wit tenue. Ook alle machines en equipment werden wit geschilderd.
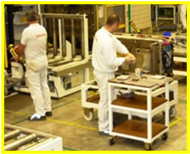
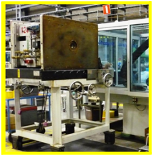
Letterlijk en figuurlijk werden muren afgebroken en poorten geopend, en enigszins onverwacht werd net als de ‘spare-parts-on-hand’ ook de benodigde ‘floorspace’ gehalveerd. De compactheid van de flow dwingt ons om er nooit een matrijs uit te halen, met het risico om dan ‘vergeten’ te worden. En bij een spoedgeval zetten we 2 of 3 technici in ipv 1. Dit om de job alsnog sneller geklaard te krijgen.
De graad van TPM kan worden gemeten door de productie-uptime. BEFORE was die <60% en die is AFTER gestegen naar een 82%. World class OEE-level van 85% is zo niet ver meer af.
De output van de toolshop is nu vertienvoudigd. Waren er BEFORE in de toolshop 9 specialisten (helden 😉), dan zijn ze AFTER nog met 3 multi-skilled techniekers. Alle verbeteringen in toolshop opgeteld levert ons dit een zelden bereikt resultaat op:
Productiviteit = x30 !!!
BEFORE was er onverschilligheid, afstandelijkheid, en niemand was gelukkig in hun samenwerking. AFTER wordt er relax gewerkt in de toolshop en vertrouwt men in productie op een prompte en performante dienstverlening.
BEFORE bleef ons service level vaak onder 84%. AFTER hikken we tegen de 96% aan. Kaizen doel bereikt. "Job well done”
Misschien wel de leukste ‘reward’ kregen wij later van sensei Kurusaka. Hij ging een filmpje van onze TPM als ‘best practice’ presenteren bij … jawel, TOYOTA.
Stay in the loop!